Table of contents
Tunable White PWM 24V LED Spots
Expert Vision introduction
Development of Tunable White 24V LED Spots
Introduction
We have been developing products related to dim-to-warm LED lighting since 2015. Initially, there were only a few KNX and DALI LED tunable white Controllers available, with the main controller product designed for single CCT or DT6 protocol. To align with mainstream controllers, we developed products that adhered to the highest technical standards at that time. Now this product is widely used in AKD LED Controller by MDT Electronics, and its dimming performance has been fully verified.
Challenges and Solutions
However, we encountered limitations with the available LED COBs (Chip-on-Board). The only COB on the market, sold by Sharp Corporation of Japan, had a CRI (Color Rendering Index) of only 80, which did not support color temperature customization and did not meet our brightness standards. To overcome this, we collaborated with our partners to develop COBs with 2 CCTs (Correlated Color Temperatures). Additionally, we designed a specialized and Original circuit driver to enable constant voltage PWM (Pulse Width Modulation) signal input with 3 lines.
Optical Solution
Due to the nature of the dual-color temperature LED light source, the position of the emitting LED would change when adjusted and controlled. Using a lens as the optical solution was not suitable as it resulted in color stratification, leading to poor dimming and color matching experiences for users. To mitigate these adverse optical effects, we developed a new optical system. This unique design quickly gained popularity in the market, positioning our products advantageously in 2015.
Key Components 24V LED Spots Construction:
The foundation for creating a high-quality product lies in using the right components of the highest quality. We collaborate closely with engineers and manufacturers of the individual components that make up the LED Modules, including LED chip manufacturers, LED packaging companies, PCB manufacturers, and heat sink raw materials.
LED Chips:
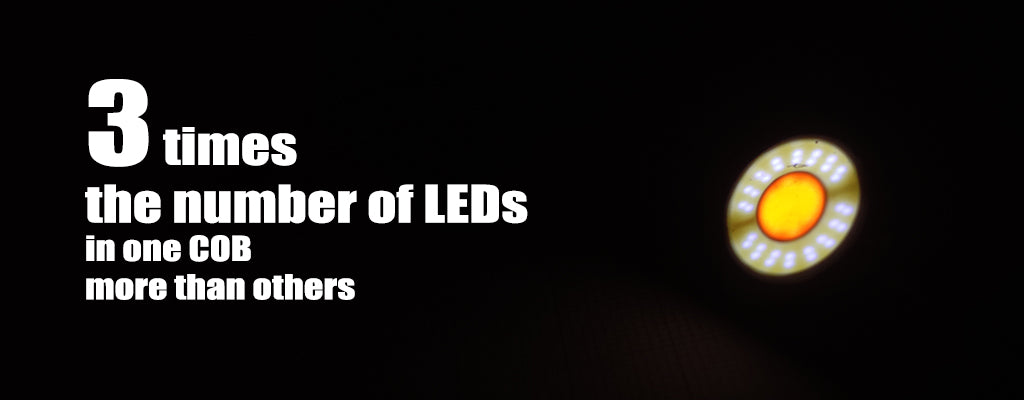
COB packaging process:
To achieve the best light effect and light color, we do not just purchase the common COB directly from the market, but directly cooperate with LED Chip and LED packaging manufacturers to develop. In the selection of Chip, we use the largest size chip, which can emit more light under the same current. We also worked on details elsewhere.
In addition to high light efficiency, high color rendering is also a place we are very concerned about. As the one of LED lighting manufacturers to develop and manufacture high CRI, we have also made great efforts. To make the color of the light more near natural light, we not only care about CRI but also make corresponding requirements for the Planck curve and TM30. Every COB of us needs to meet a very high requirement.
So we are very confident that if you compare our product directly with other similar products, we will give you a great feeling.
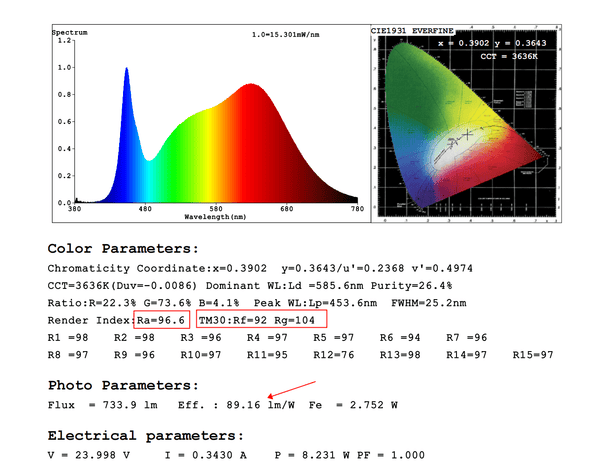
Specialized circuit driver:
To solve this problem, our drive circuit is specially designed with a constant current circuit. Under certain line loss and voltage drop conditions, the circuit can provide consistent current, ensuring that there will be no problem of inconsistent brightness between two LED spots that are relatively far apart.

From Above Testing, we could easily know, in 23-26V Voltage input, the total current of LED Spot are same, so whatever voltage loss or Overvoltage, our spots can keep the same brightness
Additionally, the constant voltage PWM dimming method achieves dimming through continuous switching. However, the rapid on-off of the voltage can damage the integrated chips and LEDs due to the sudden change in current. To address this issue, we have added a special filter circuit to the circuit, providing a very good solution to the pain points of the industry.
Good Heat dissipation:

Why is it often advertised on the market that the LED lifespan can reach 50,000 hours, but the actual lifespan of lamps is not?
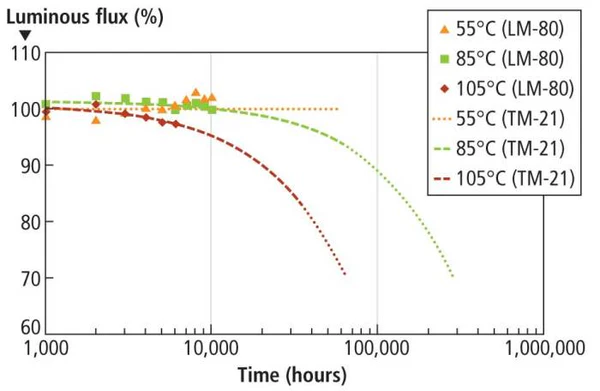
To answer this question, we need to know a basic knowledge. The lifespan of all semiconductors and electronic materials will be affected by temperature. Different operating temperatures bring different lifespans. As shown in the figure above, the life of LED changes with temperature. When the LED temperature is 55℃, we can see that its life curve can be maintained at a certain level. When the temperature reaches 105℃, after 10000hrs, its life curve The life curve drops rapidly. Therefore, the LED lifespan advertised on the market is as high as 50,000hrs, which refers to the test results of its working temperature at 25°C, which is an ideal laboratory test data. In addition, in addition to LED chips, there are other materials in COB, such as gold wires used to conduct electricity, glue for fixing LED chips, etc. The lifespan of the materials will be affected by temperature.
From the above information, we can know that we hope that the longer the life of the LED, the better the heat dissipation performance of the LED lamps. And better heat dissipation performance means higher manufacturing costs, so not all LED manufacturers are willing to do this. , they often only control the temperature of the LED at 105°C to control costs.

The test results are: 24V voltage input, dual channels reach maximum power, light up for 20 minutes and the temperature no longer rises.
For actual engineering practice, it is almost impossible to control the temperature at 25°C, or the cost of achieving this goal will be very expensive and cannot be accepted by the market. As an LED Spot manufacturer, TILLUME can only choose high-quality raw materials as much as possible to increase the design margin and optimize the heat dissipation design to reduce the operating temperature of the LED Spot. This is also the main reason why TILLUME chose the above-mentioned high-quality materials and customized chips. The purpose is to control the temperature of the LED Spot to achieve the goal of longer life. However, because our business model is that manufacturers sell directly to the end market, we reduce many intermediate links and make our prices more friendly.
In addition to the COB factor, there is another important component that is also affected by temperature, and that is the built-in LED driver circuit. Sometimes the failure of LED Spots is not due to the end of the life of the COB, but due to the failure of the internal integrated circuit, which causes COB failure. For this reason, TILLUME uses aluminum PCB for its internal circuit to better take heat away from the IC. And if you are careful, you can notice that our back is flat and is not fixed with screws. The purpose is to allow the PCBA to be well connected with The external heat sinks are in contact, thereby reducing the operating temperature of the drive. Although such a design has certain requirements on the manufacturing process, it can effectively dissipate heat. Although the manufacturing difficulty is greatly reduced by using screw fixation, the driver board can only be placed in the inner cavity of the radiator and cannot fit perfectly with the radiator. The heat dissipation situation will become worse, even if the glue filling process is used. The heat transfer performance will also be greatly reduced due to the low thermal conductivity of the heat dissipation glue.
Lens or reflector?
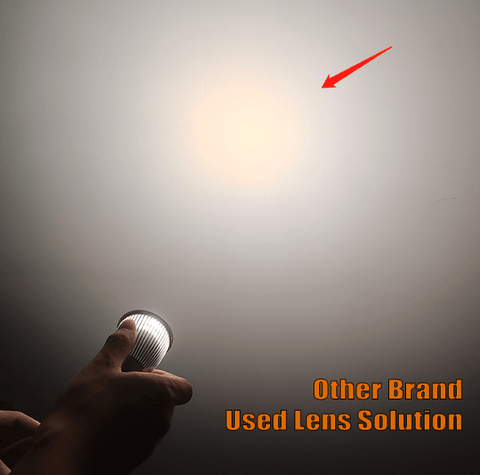
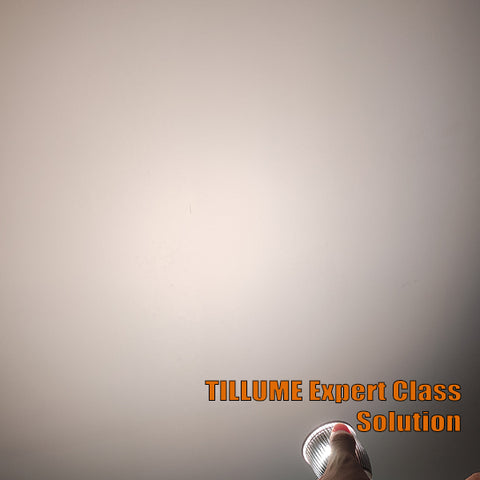
From the photo comparison, you can find use a lens to make DTW LED spot, there has a light spot in the center whose color is not the same as the outside. When you adjust CCT, that will be a bad experience you find there have 2 kinds CCT in one room, but not the CCT you want.
For this reason, we designed a part that mixes light of different colors, which can easily mix the light in different directions into a light ball, and then re-reflect the light of the light ball through the reflector to achieve the solution. stratification problem.

In addition, the reflector selected by TILLUME, adopts the aluminum spinning process with a relatively complicated manufacturing process, which can not only reduce the occurrence of glare. At the same time, when used for a long time, the metal material itself will not turn yellow like the plastic material, which will change the light color.
The Strict Quality Control Process
From the inspection of raw materials, we have begun to work carefully. For very important parts, our sampling ratio is much higher than the general level of the market. To ensure color consistency, TILLUME control Macdam within 2 steps, and then we also select and sort LED Chips to ensure consistency between batches.
Even in appearance, we strive for excellence. Every production process has strict standards. We do not pursue productivity improvements to reduce our manufacturing costs. Every step needs to be carefully crafted.
We know that the user's use environment is very different. To ensure the reliability of the product, each lamp needs to go through an aging process of up to 12 hours to ensure that each product shipped is good enough.